The theoretical energy density of Zn-Br batteries is quite astounding. We can calculate this value for a given concentration of electrolyte by calculating the amount of ZnBr2 in one liter and then using Faraday’s constant and the expected output voltage (1.85V). Considering that each Zn atom is able to transfer two charges, we are left with this equation:
Theoretical Energy Density (Wh/L) = 1.85 * Molar Concentration * 2 * 96485.3329 / 3600
If we graph the theoretical energy density as a function of the concentration we get the plot below:
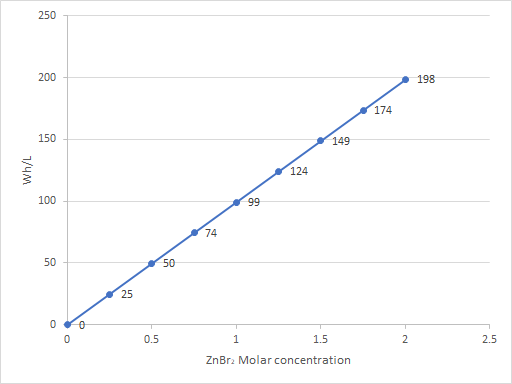
Notice that if we could use all the Zinc in a solution, it should be pretty straightforward to get 50 Wh/L from a solution containing only 0.5M of ZnBr2. However, in practice most static and flow batteries use ZnBr2 solutions in a 2-3M concentration range and are able to only extract around 35-45Wh/L. Why aren’t we able to extract the 150+ Wh/L that is promised by the plot above at these concentrations?
The reason has to do with the conductivity of water, the migration of ions and the voltaic losses suffered by the battery. As we extract ions from an aqueous solution of ZnBr2, the electrical resistance will increase, as the solution becomes less conductive. This means that the voltage required to inject charges increases from the theoretical minimum – 1.85V – towards much higher values. As the solution becomes depleted of Zinc and Bromide ions it will also take much longer for ions to move across the battery and reach the electrode where they can be deposited, leading to further voltaic losses. If the battery is charged or discharged at higher currents, the above processes will be even more inefficient – as side reactions will happen – which will lead to even less efficiency.
Adding supporting electrolytes can help with the conductivity problem, but it will still not help a lot since the supporting electrolyte will lack either Zn or Br ions – or both – which will still limit the battery charging by how quickly these ions can migrate. In the end we are left with the need to use ZnBr2 itself as a supporting electrolyte, forcing us to create batteries that use only a fraction of the potential energy in the battery – around 10-30% at most – in order to prevent all these problems from being important.
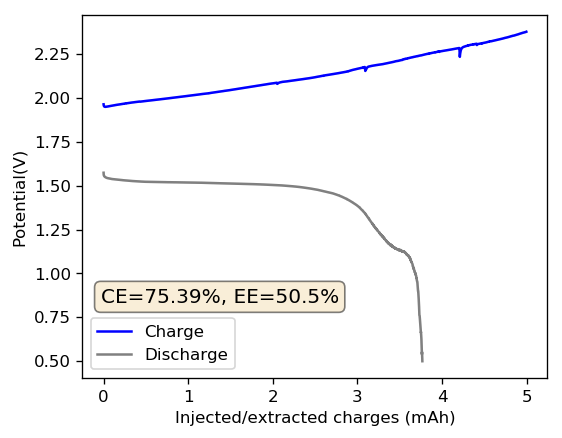
The plot above shows you what happens experimentally when we run a battery with 0.5M ZnBr2 saturated with TMPhABr (to sequester Bromide ions in the cathode) with a GFE-1 cathode pretreated with a 10% TMPhABr solution (saturated, then dried in air). In practice when we charge the battery to 5 mAh at 5mA we see a big increase in the charging voltage – because of the above mentioned voltaic loses – and the discharge curve shows our average voltage is only around 1.45V due to the higher resistance of the solution when we start the discharge process. In the end the energy density is only around 8.5 Wh/L, around one fifth of the capacity that we expected. The energy and coulombic efficiency values of the battery are also pretty low, as a lot of charges and energy are lost in the charging process.
The propensity for additional side reactions also means that there is going to be degradation in the organic materials and hydrogen evolution, both which will also increase the charging potential more and more with each cycle and lead to very premature death of the battery.
Because of all the above reasons, practical batteries are expected to have ZnBr2 concentrations of at least 2-3M and, even at these concentrations, it is unlikely for the energy density values to exceed 45-50 Wh/L. It might be possible to reach higher densities at higher concentrations but then we are left with a lot of additional problems, including higher dendrite formation and lower solubility of many elemental bromine sequestering agents, both things that are likely to kill the battery, making it unlikely that it will reach the expected higher density. Because of the above, a battery in the 2-3M ZnBr2 range that can substantially avoid dendrites and self-discharge is most likely the best that can be achieved with Zn-Br technology, either in a flow or static configuration.