An important issue with Zinc-Bromine batteries is the need for a high purity Zinc Bromide solution in order for the battery to work properly. The use of low-cost ZnBr2 sources, in particular the use of Zinc Sulfate and Sodium Bromide to generate Zinc Bromide solutions, can be problematic due to the presence of large amounts of Iron impurities. In this post I will discuss what happens when you have these impurities in a battery and how you can purify a Zinc Bromide solution to remove iron and achieve better results.
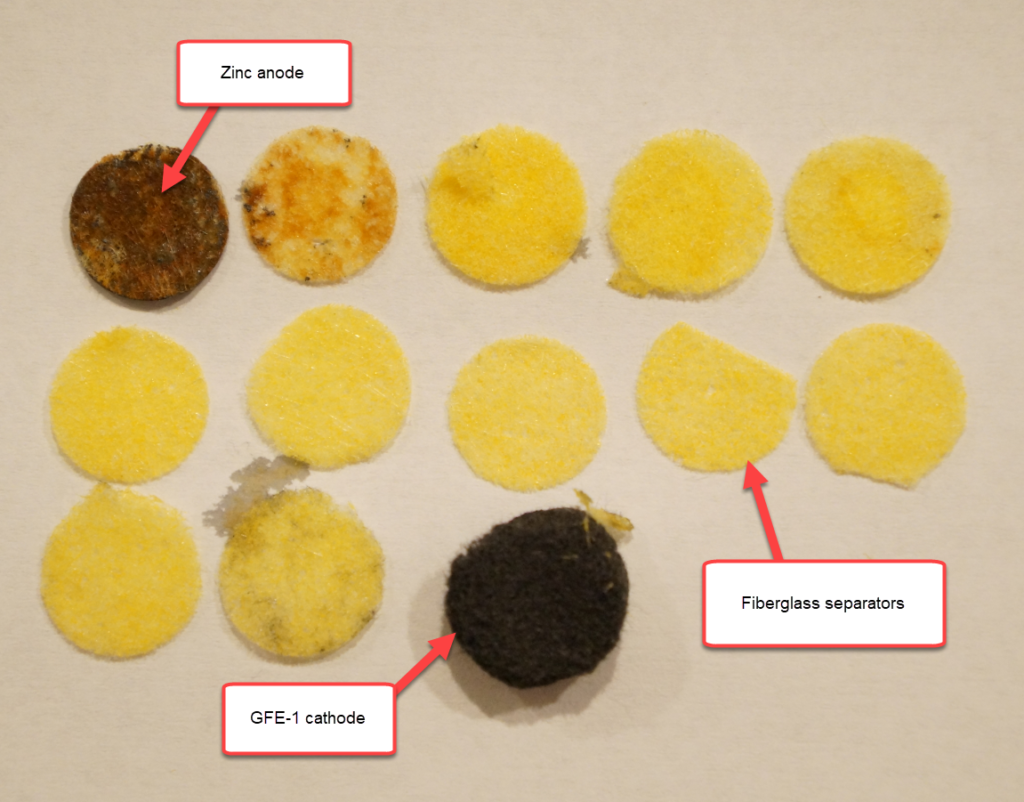
The image above shows you the layers of a Zn-Br battery that was taken apart after 15 cycles, charging the cell to 15mAh at 15mA and discharging to 0.5V, the cell has a diameter of half an inch. As you can see, the fiberglass separator layers look very yellow and, although it would be tempting to assign this color to the presence of elemental Bromine, which is true in part, cells constructed with high purity ZnBr2 solutions do not show such a strong yellow coloring. The yellow color is in large part caused by the oxidation of Fe+2 to Fe+3.
Moreover, the Zinc anode is usually a grey or black color in batteries created with high purity ZnBr2 solutions, while in this case, it looks a lot like a rusted piece of Iron. This is no coincidence, as Fe is actually reduced in the anode and then oxidized to insoluble Fe oxide/hydroxide species. The first two layers of the battery show the strong presence of these red Fe+3 oxides, which are non-conductive and significantly hamper the performance of the battery.
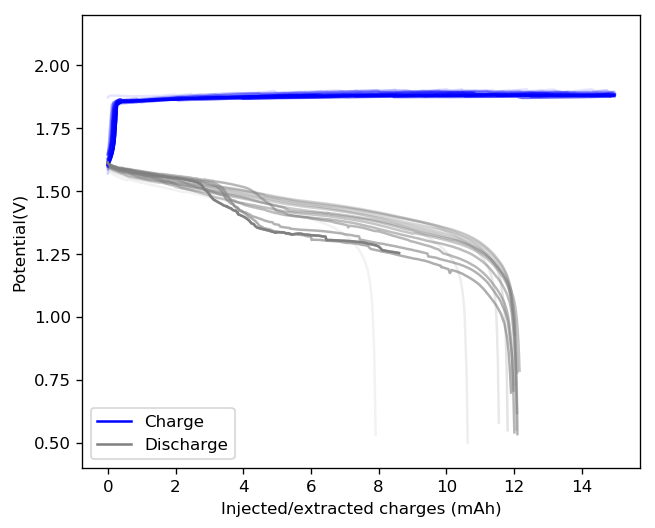
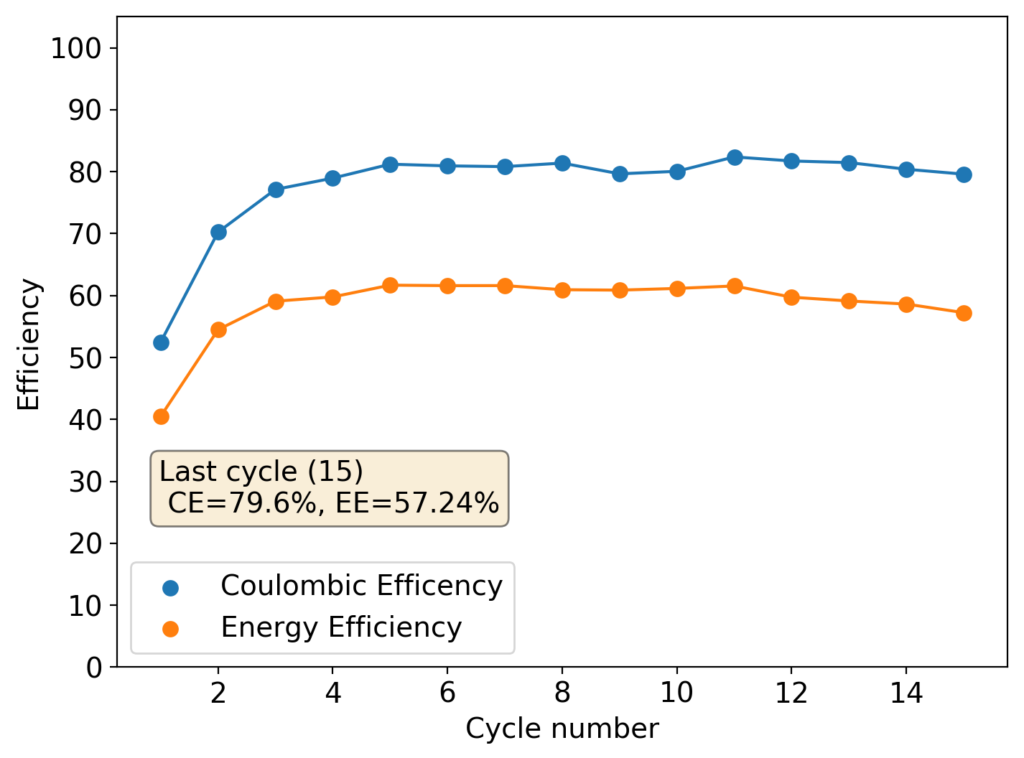
The characteristics of this inverted battery were actually not bad to begin with, achieving max CE and EE values of 81% and 61% respectively. However the discharge curves start showing significant deterioration around the 10th cycle, with strong drops in the discharge voltage around 3-4 mAh into the discharge cycles. This was also shown as a strong decay in the average discharge potential, which during the 15th cycle was around 6% lower than the starting value. This speed of decay is dramatically faster than for Zn-Br batteries created using high purity ZnBr2 solutions.
The above implies that you need to get rid of these Fe impurities if you expect to be able to run a Zn-Br battery that lasts for a long amount of time. Thankfully there is a pretty easy way to do this, which we know from the literature surrounding the purification of Zinc brines (see here). The trick is to use a 3% hydrogen peroxide solution for the preparation of your ZnBr2 solution, instead of distilled water, when you dissolve the Zinc Sulfate and Sodium Bromide salts. This causes all the Fe to be oxidized to Fe+3 and to precipitate out of solution.
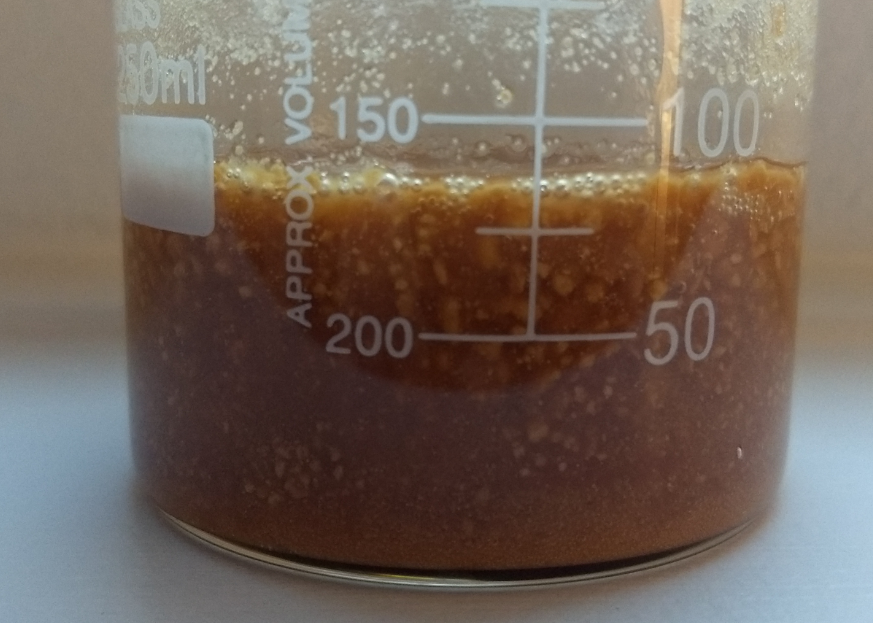
The image above shows you how this reaction looks. The Fe compound generated is very red, while the precipitated sodium sulfate is white, giving you this sort of look. The reaction takes around 6 hours to fully complete – for all the Fe to be precipitated out – time after which you can filter the solution and measure the density of your resulting brine to figure out what approximate concentration you have (per my previous post). It’s crazy how much Iron the “high purity” agricultural grade Zinc Sulfate Monohydrate contains!
It is also worth noting that this ZnBr2 solution will contain a significant amount of peroxide so you either need to heat the solution up to fully decompose the peroxide or wait till all the peroxide is decomposed at room temperature before actually using the solution in a battery. To be absolutely sure, you can also use H2O2 testing scripts (like these), to figure out whether you have any peroxide left before considering a solution to be battery-ready.
With that said, this process is absolutely necessary to build Zn-Br batteries if you’re deriving your Zinc Bromide from an impure source, as a Zn-Br battery containing large amounts of Fe will degrade and stop working pretty fast as a function of time. If you want to test your ZnBr2 solution you can add a couple of drops of H2O2 to a sample of it and see if any Fe precipitate forms.