In the past I have discussed zinc dendrites as one of the most important issues to deal with when creating Zn-Br batteries. While the effect of dendrites can be attenuated by using tall cells with large distances between the electrodes, these setups create high electric resistance that greatly diminishes energy efficiency. A high energy efficiency Zn-Br battery will therefore have the ability to reduce or eliminate zinc dendrites, such that a large number of cycles can be achieved without shorting the battery.
I have studied the use of PEG-200 quite extensively within this blog and although PEG-200 does reduce the formation of zinc dendrites, it also increases the internal resistance of the battery, to the point where the voltaic losses become unacceptable. At useful energy density values (>30 Wh/L) and acceptable charging currents (>10 mA/cm2), the maximum PEG-200 concentration for a 3M ZnBr2 solution is therefore restricted to around 1-3%.
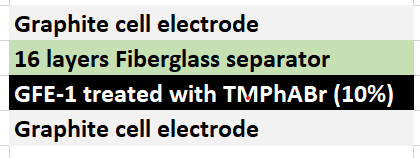
Looking at other potential low cost solutions to eliminate zinc dendrites, this article using PEG and Tween 20 in alkaline batteries drew my attention. Although the article used PEG-600, it is reasonable to expect a similar effect with PEG-200, given that this has also been shown to reduce Zinc dendrites in alkaline batteries in multiple publications. It is particularly interesting that they can achieve this with a 0.5% PEG-600 + 0.5% Tween 20 solution, as this would be of practical use within Zn-Br batteries.
To investigate this, I bought some USP grade Tween 20. It is a very safe , non-ionic surfactant commonly used commonly for cosmetics. I then prepared a solution using ~1% PEG-200 and ~1% Tween-20 with 3M ZnBr2. I then assembled a battery as shown above. Note that although I have been using a separator-less setup during the last couple of weeks, I decided to try a fiber-glass based separator setup first, since this setup in the past suffered from dendrites at the edges that I believe might have been caused by surface tension issues with the solution. This problem is likely to be solved by the use of the Tween 20.
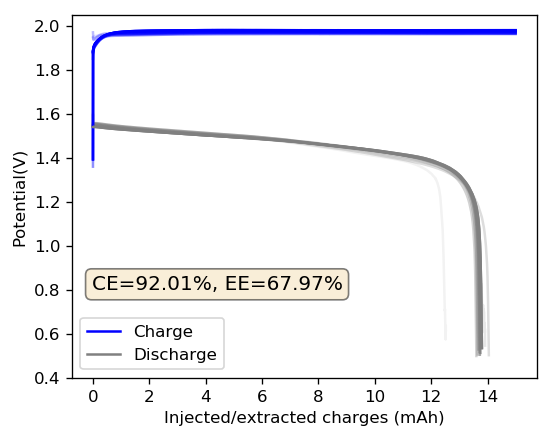
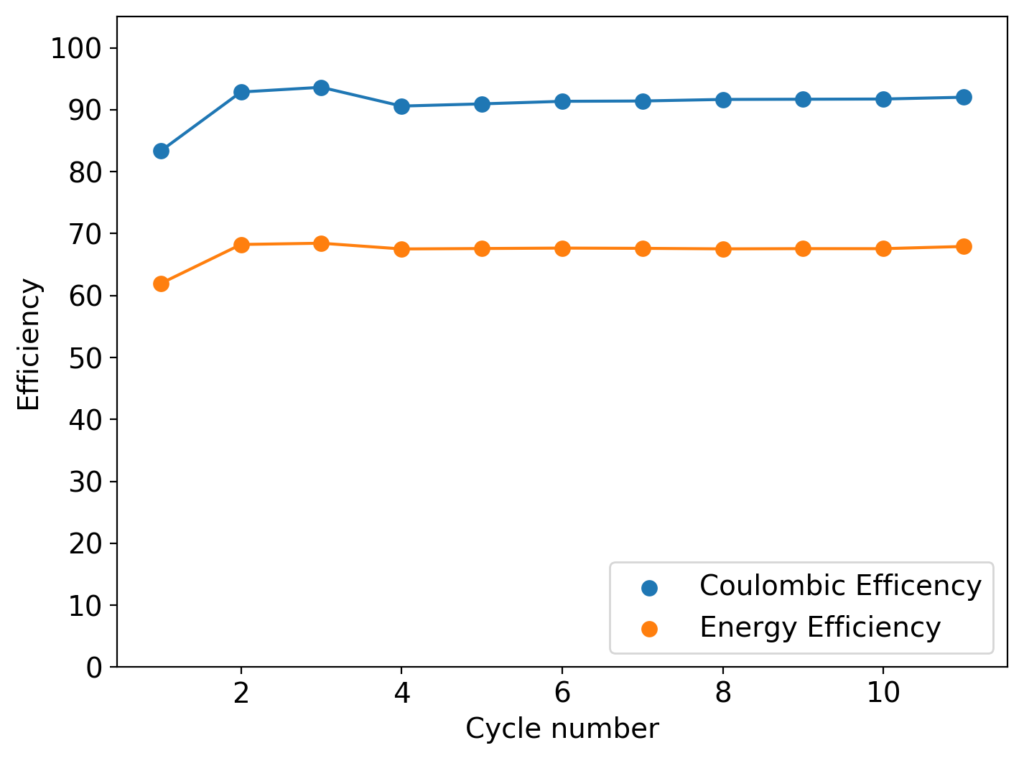
The solution was easy to prepare and the Tween 20 did not generate any solubility issues. The assembly of the cell was quite interesting, while a 3M ZnBr2 solution (with or without PEG-200) normally takes around a minute to fully wick into the fiberglass separator and the GFE-1 cathode, this time the wicking was almost instantaneous, probably thanks to the use of the Tween 20, that greatly reduced the surface tension of the mixture.
The cycling of the cell is going on without any issues. After around 3 cycles, the magnitude of changes in the shape of the curves and capacity started to become smaller and smaller, with the battery currently settling at a CE ~ 92% and an EE ~ 68%. The total amount of charge extracted is around 13.8 mAh with an average potential of 1.46V, putting the energy density of the battery at this current density at around 30 Wh/L. I am so far amazed at the stability of this battery configuration with few aberrations showing in the charge/discharge curves and no signs of dendrites (so far). The above are the first ever published results – as far as I know – for a Zn-Br battery containing both PEG-200 and Tween 20.
An important early sign of dendrites is a decrease in the charging potential with time – as the zinc dendrites effectively enhance the surface area of the anode before shorting the battery – an effect that I haven’t observed after 11 cycles. Although still too soon, the above results are certainly encouraging, hopefully the synergistic effect between PEG and Tween 20 applies to the Zn-Br system as well.