As I’ve mentioned in previous posts, tetrabutylammonium bromide (TBABr) is not a very good sequestering agent for static Zn-Br batteries due to its very low solubility in Zinc Bromide solutions. To solve this problem, I have decided to test trimethylphenylammonium bromide (TMPhABr) as a potential replacement, since this salt also forms and insoluble perbromide but – due to its significantly higher polarity and lower molecular weight – should be significantly more soluble than TBABr. I ordered it from Alibaba around one week ago and recently got it delivered.
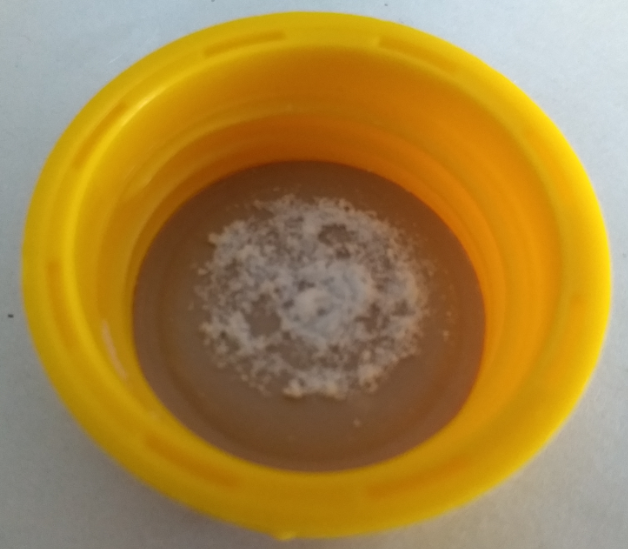
My initial tests with it involved testing its solubility in Zinc Bromide solutions. The solubility of TMPhABr in pure water is not indicated clearly anywhere, but I assumed its solubility would be similar to that of trimethylbenzylammonium bromide (TMBABr) or tetrapropylammonium (TPABr) bromide, both which have solubilities of around 10% by mass in water at 25C. My initial tests have confirmed this suspicion with solutions at 10% by mass being easy to prepare at 20-25C. I didn’t try to prepare more concentrated pure solutions as my objective is to judge its solubility in the presence of Zinc Bromide.
The first test I performed to evaluate this was a 0.25M solution of Zinc Bromide which was able to dissolve 0.12M of TMPhABr with no problems. I then increased the amount of ZnBr2 to 0.5M – which is what the authors of the Chinese paper using ZnBr2+TPABr use – and I was able to dissolve 0.25M of TMPhABr without issues. With this result I know I will be able to at least reproduce similar experimental conditions to those achieved by the Chinese researchers, something that I could never do with TBABr due to the solubility issues mentioned before.
To test how far I could take this I then attempted to prepare a 1M solution of Zinc Bromide and see if I could get 1M of TMPhAbr to go with it. Sadly at this point the concentration of TMPhABr is already too high – would be close to 10% by weight of the solution – so it was actually not possible to get to this point. This means that the practical limit of this battery will be to have around 0.25M of TMPhABr dissolved, which is probably a realistic limit for most quaternary ammonium salts since we are unlikely to get an effective sequestering agent – not electrochemically active and with no effect on pH – with a molar mass significantly lower than that of TMPhABr at a similar price point.
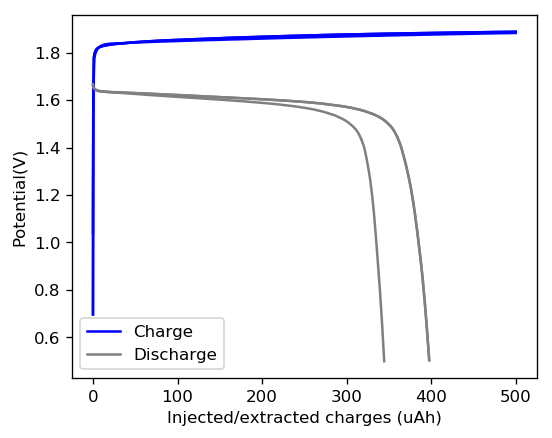
I then used this 0.5M ZnBr2 + 0.25M TMPhABr solution to create the first battery. This battery had a diameter of 0.5 inches and was built within my Swagelok cell. I used a 0.2mm thick Zinc anode followed by 8 layers of fiberglass separator and a CC4 carbon electrode. I also made sure to sand the graphite electrodes in the Swagelok cell to make sure their exposed surface was pristine. I put 50uL of the electrolyte on the cell but I won’t know how much ended up in the separator until I open the cell after testing and weight the wet components.
The graph above shows the first – to the best of my knowledge, the first ever public – charge/discharge curves of a static Zn-Br cell prepared using TMPhABr as a sequestering agent. It is very interesting to note that the shape of the discharge curve improved immensely moving from TBABr, showing that this battery is significantly better behaved. Although the CE and EE of this first curve were particularly low, the CE of the second curve measured already showed an increase of the CE to 79% and EE 66%. I will keep cycling the battery and will show you how the CE and EE change as a function of the number of cycles. Exciting times!