Zinc bromine batteries are a very interesting battery chemistry that goes back at least a hundred years (see here). These batteries are quite especial in that the battery is assembled in a completely discharged state, where both electrodes in the battery are relatively inert and all the charging of the battery is done by reducing/oxidizing materials in the liquid electrolyte into the electrodes. These batteries have the potential of high capacities with the use of very cheap materials, while having a safety profile significantly better than that of regular lead acid or lithium ion.
The battery reduces (plates) zinc into the negative electrode of the battery and oxidizes bromide to elemental bromine in the positive electrode of the battery. These reactions allow the battery to have a relatively high theoretical potential but also implies that you get elemental bromine – a highly reactive liquid – in the anode of the battery. This is one of the main complications and reasons why these batteries have never been very successful in commercial applications. The bromine is not entirely insoluble in the electrolyte – which is generally water – and can therefore migrate to the negative telectrode to react with the zinc, causing a self-discharging of the battery that is extremely detrimental to long term storage in these systems.
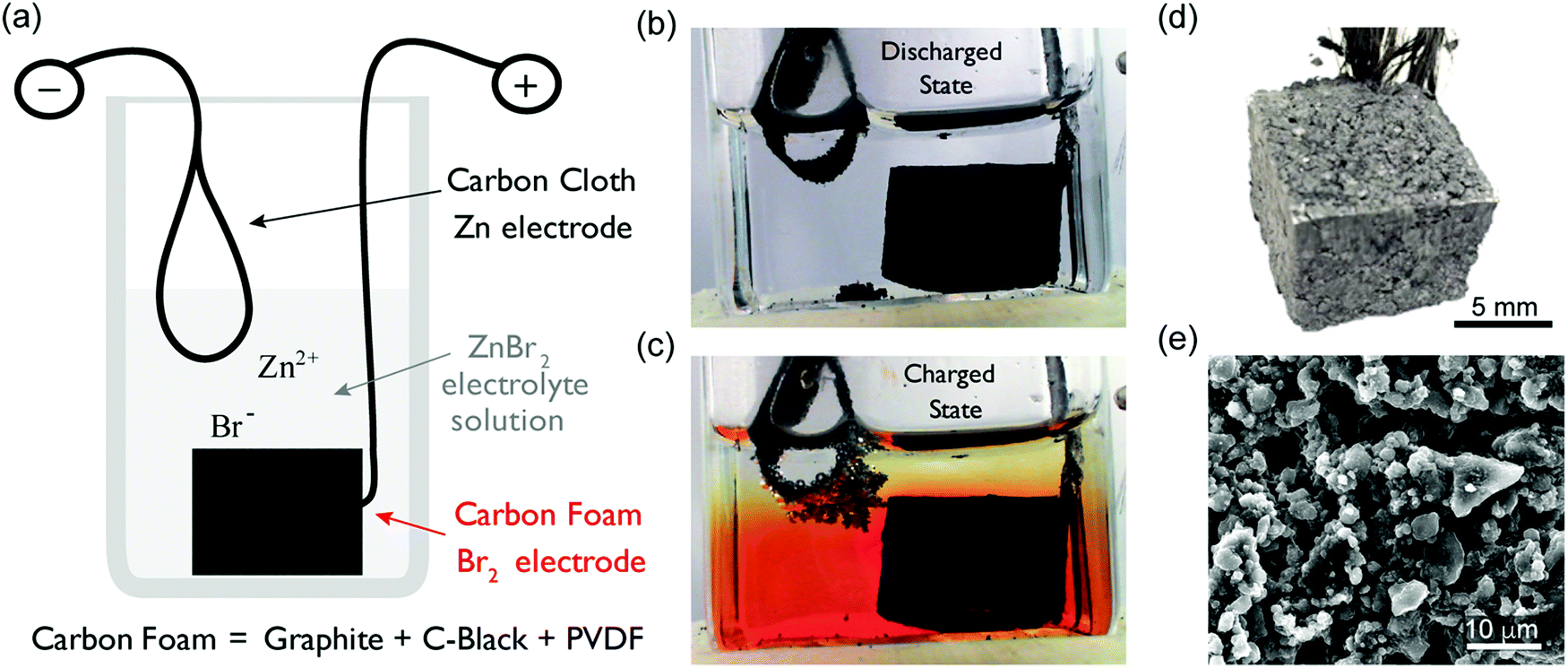
The above is why these systems have mostly been exploited as flow-batteries, because if you can take the bromine produced and just move it away from the zinc deposit, you can effectively ensure that the battery charge is preserved as a function of time. This inevitably complicates battery construction substantially, but does allow for some practical applications of the technology.
During the past few years there has been a renewed interest in this technology, first due to some Princeton articles that talked about these batteries in the context of a “minimum architecture” battery (see here) but this actually just reproduced some of the earlier results of this technology and does not provide substantial solutions to the problems associated with self-discharge in these systems. They however point to the fact that these problems can actually be relatively inconsequential if the batteries are used for mass storage and the actual time the energy needs to be stored for is low. The fact of the matter is that the self-discharge reaction in these batteries is not destructive for the battery, just a waste of energy, contrary to other battery chemistries where self-discharge can generate problematic issues that kill the batteries themselves. The point being, if you need to store the energy for a short time and you can waste some, this is your chemistry.
However some people realized that the problem of self-discharge could be reduced substantially by using some substances that capture the Bromine produced into insoluble tribromide salts. This is what some smart people from China did (see here) using TPA (tetrapropylammonium bromide). The introduction of this chemical into the battery chemistry allows tetrapropylammonium tribromide to form in the positive electrode of the battery – instead of liquid bromine – which substantially prevents the reaction with the zinc on the other electrode as these salt is significantly more insoluble than the bromine.

The image above, which contains some of the results in their paper, shows that Zn-Br technology, when used in this manner, has the potential to have specific energy and power values that can rival even modern lithium ion technology. Furthermore, the cost of all of the materials involved here is relatively low, although these Chinese experiments did use a fancier carbon electron for their positive electrode.
Looking at what the Chinese did, I wondered if it would be possible to create a battery that reproduces their results, with some materials I could find online. I found a carbon felt from ceramaterials with high conductivity and surface area, you can buy an A4 sized sample for less than 50 USD and coupled this with some conductive HDPE, a copper mesh and copper tape. Since zinc can be plated onto carbon felt as well (see here) I decided to go with a construction mechanism where both of my battery electrodes will be constructed from the same material. For the separator I decided to go with a fiberglass separator, the best one I could find for the purpose was this tissue. In order to enclose the battery I decided to go with some shrink tubing, since I could easily seal the ends with a little bit of heat.
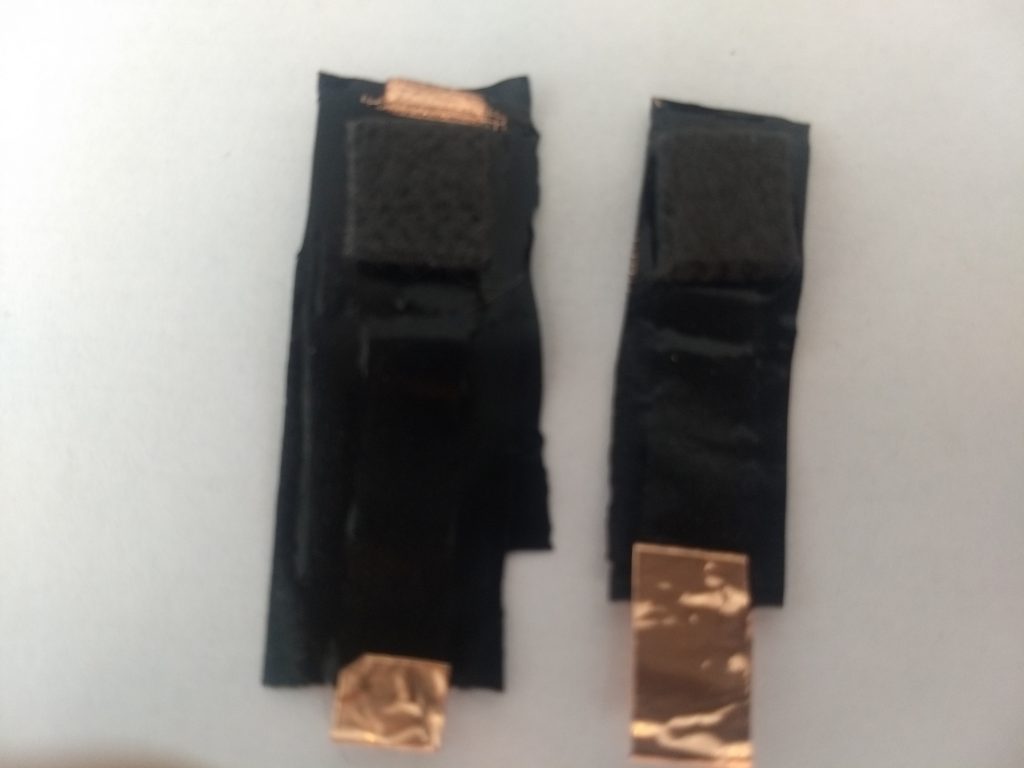
The electrodes are made by heat pressing HDPE to the carbon felt using a regular iron (with some wax paper to prevent it from sticking to the iron) then heat pressing the copper mesh onto the HDPE, then putting the copper tape on the mesh and finally pressing another layer of HDPE to seal all the components in. The resistance measured between the copper and the felt in these electrodes should be lower than 1 ohm, meaning you should be easily able to measure continuity between them.
To build a battery two of these electrodes are put together with 4 layers of the fiber glass between them – it’s pretty large pore so using 1 or 2 layers often caused shorting issues between the carbon felt electrodes – and then placing that inside the shrink tubing. I then sealed the sides of the tubing using a regular iron to ensure everything was enclosed.
The next step is to prepare the solution, for which I used a class A 10mL volumetric flask and prepared a 0.5M solution of Zinc Bromide and tetrabutylammonium bromide (TBAB). Notice that I used tetrabutyl, not tetrapropyl, since this is more readily available. Both of these substances were bought on ebay or amazon, although they are more expensive than they would if you bought them in bulk quantities. The solution is then injected into the tubing using a needle and the hole is then sealed using regular electrical tape (usually I open to holes to allow air to go out of one). The above solution had some solubility problems (the TBAB wouldn’t go into solution at this concentration) so some of my future experiments will test out different concentrations.
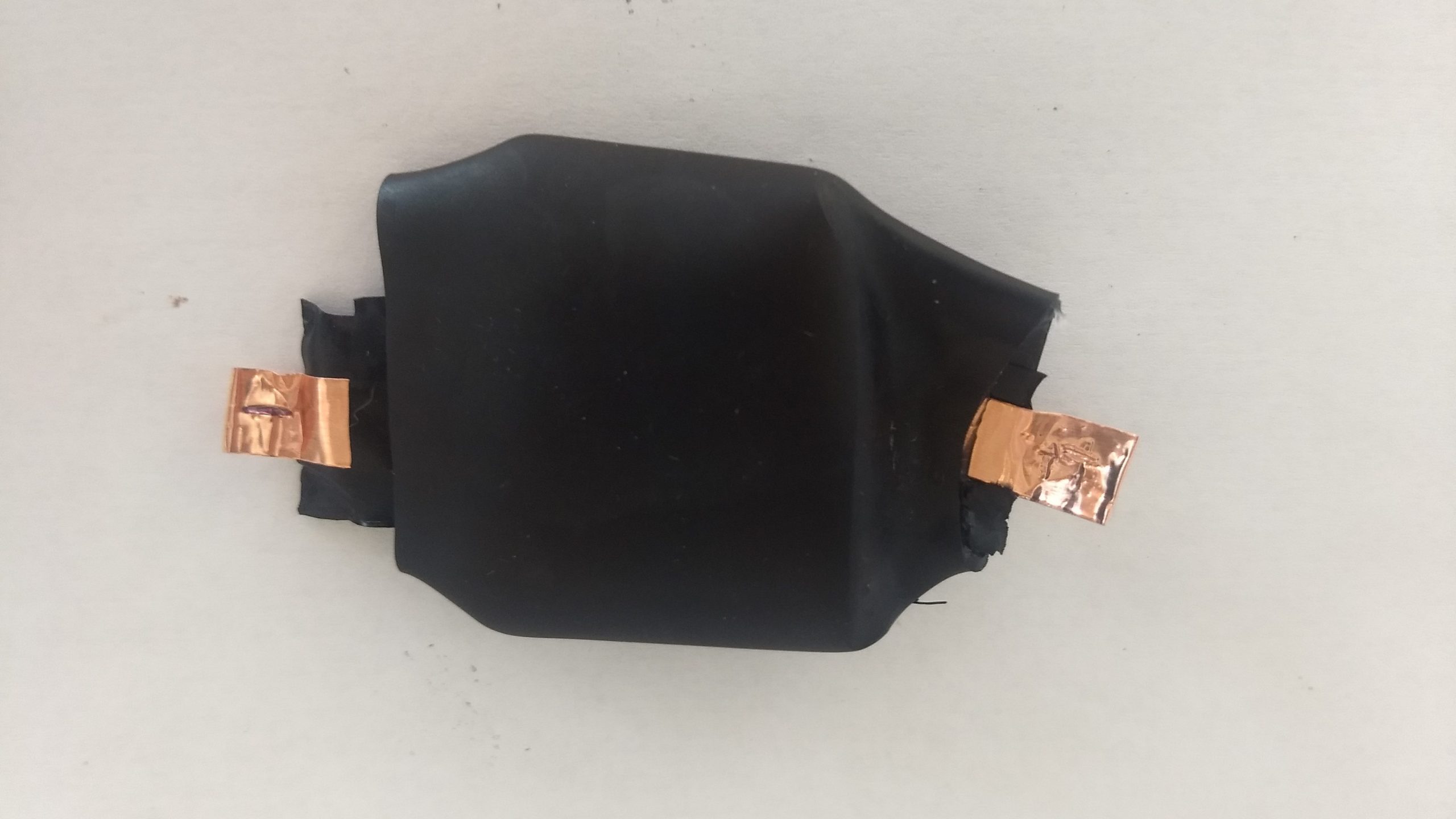
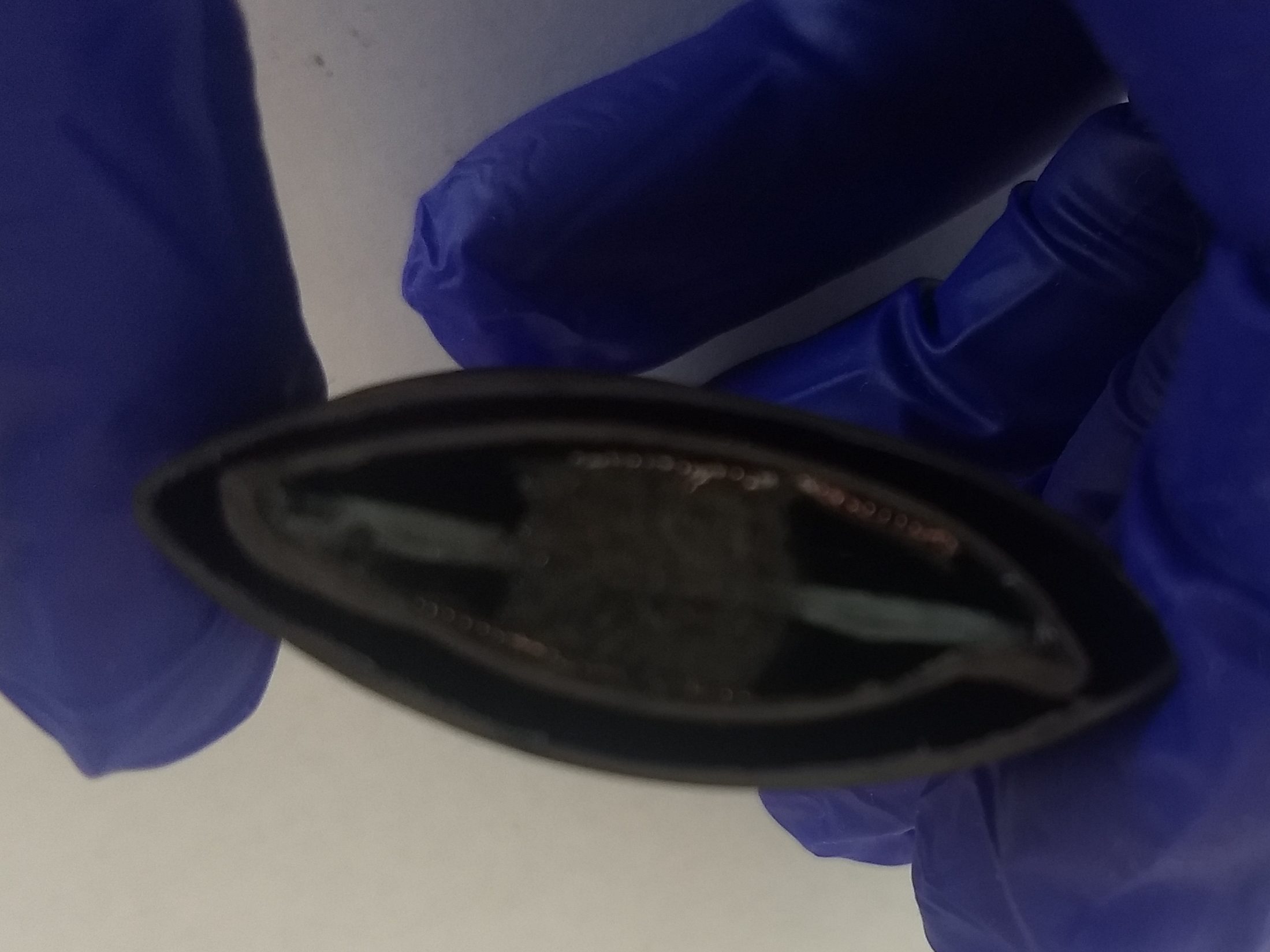
I have already started testing some of these batteries and look forward to sharing some of their actual electrochemical results within a future post. As a sneak peak I can tell you that the coulombic efficiency of these cells is greater than 92%. But you will see much more, including charge/discharge curves and other tests, really soon!